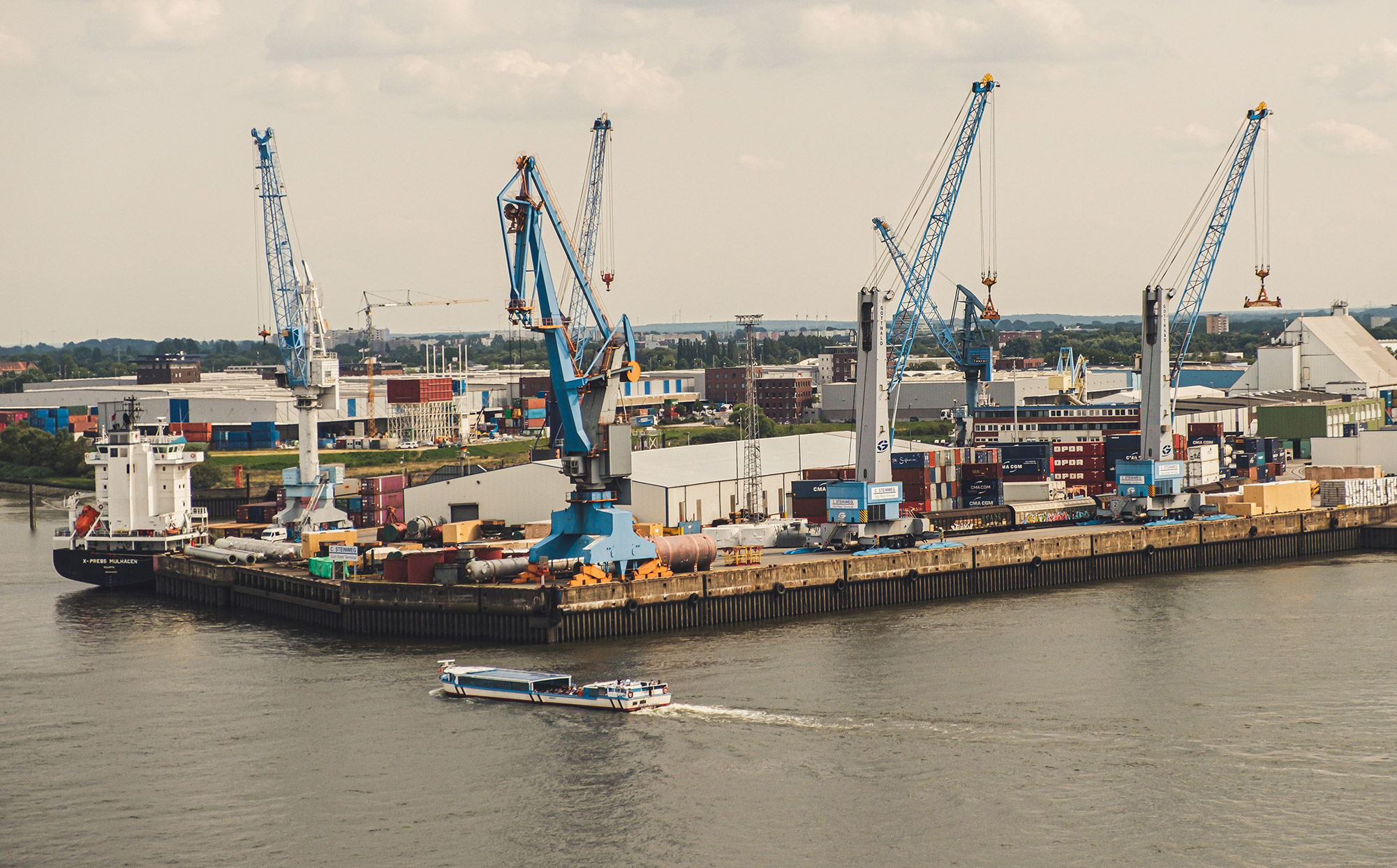
Is carbon neutrality and resource wisdom in a gated industrial area too narrow a perspective?
A resource-wise and carbon-neutral maritime industry network
reduce, reuse, recycle
The project developed an optimal operating model for flows of materials, resources and information in the Blue Industry Park and Turku Shipyard. The model can be used to achieve resource wisdom and carbon neutrality throughout the supply chain.
- 20–30% increase in value-adding operations.
- 3–7% reduction in material loss.
- 20% better production turnaround time through supply chain transparency and management.
- 5% lower material costs through centralised procurement.
This solution is right for you if
- you operate in the supply chain of Turku Shipyard;
- you operate in a manufacturing industry supply chain;
- you want to streamline your supply chain operations.
BASIC FACTS
- Location: Perno district, Turku. Next to Turku Shipyard.
- Industrial area life cycle: planning phase
- Organiser: Blue Industry Park Oy.
- Time span: 5–10 years from 2021 onwards.
- 600 companies in the supplier network.
- The maritime industry network in southwestern Finland employs 11,000 people.
- The turnover of the maritime industry network was EUR 3.3 billion in 2019.
The aim is to increase the efficiency of the maritime industry network
The concept identified how the operations of the maritime industry network could be streamlined, and an operating model was created for the planning and implementation of these improvements. The aim was to optimise the material, resource and information flows between the Blue Industry Park (BIP) and Turku Shipyard. The project assessed what kind of operating methods the companies in the maritime industry network should use in order to make the network’s operations as resource-wise and carbon-neutral as possible. Finally, it was determined what kind of control system would support resource-wise and carbon-neutral operations.
The logistics centre offers the best support to resource-wise and carbon-neutral operations
The concept determined which activities should be located in the BIP area in order to make the maritime industry network as efficient as possible and to support resource-wise activities. The key functionalities were production facilities and the logistics centre.
The need for production facilities varies: some operators require a small workshop while others need a larger production facility. The premises to be built must also be adaptable so that they can meet the changing demand. Pre-assembly and modularisation would also reduce the logistical burden in terms of traffic volumes and packaging materials. Traffic volumes are reduced when larger entities are transported and there are fewer deliveries of parts and components in the area.
Recycling reduces material waste
Recycling packaging waste and standardising transport packaging in the area would be very beneficial. If standardised methods were used for recyclable packaging materials, logistics operations would be clearer and the volume of packaging materials in the area would be reduced.
Building a centralised recycling centre in the BIP would serve companies in the area and help ensure that waste materials are recycled. The recycling centre would operate in the area between the BIP and the shipyard, which would be ideal for all parties.
With regard to the location of functionalities, traffic going into the shipyard must also be considered. The logistics centre should be located either beside or in the immediate vicinity of the production facilities in order to avoid any unnecessary traffic.
Information creates trust
Yhteistoiminnan ja resurssiviisauden edistämiseksi tarvitaan mitattua tietoa. Konseptiin liittyen määriteltiin viisi tärkeitä mittaria:
Measured data is required to promote collaboration and resource wisdom. Five important indicators were identified in relation to the concept:
- Security of supply of incoming materials
- DIFOT (Delivered In Full and On Time)
- Security of supply of site-specific material packages
- DIFOT (Delivered In Full and On Time)
- Progress of the site-specific plan
- Timing and accuracy of master production scheduling
- Timing and accuracy of detailed planning
- Implementation of the plan content
- Monitoring deviations
- Work package-specific monitoring
- Delivery line-specific monitoring
- Monitoring of transport volumes
- Monitoring of inbound logistics
- Monitoring of reverse logistics and material loss, surplus/waste
- 3R strategy (Reduce, Reuse, Recycle)
TAKE-HOME MESSAGES
- Material wisdom: centralised materials management can reduce material waste.
- Resource wisdom: minimising the amount of surplus material with more careful planning.
- Information wisdom: the information flow generated by the digital platform enables supply chain management and development.
“Stopping structural waste is the only way to save the planet.”
–Ari Viitanen, HPJ CarinaFour