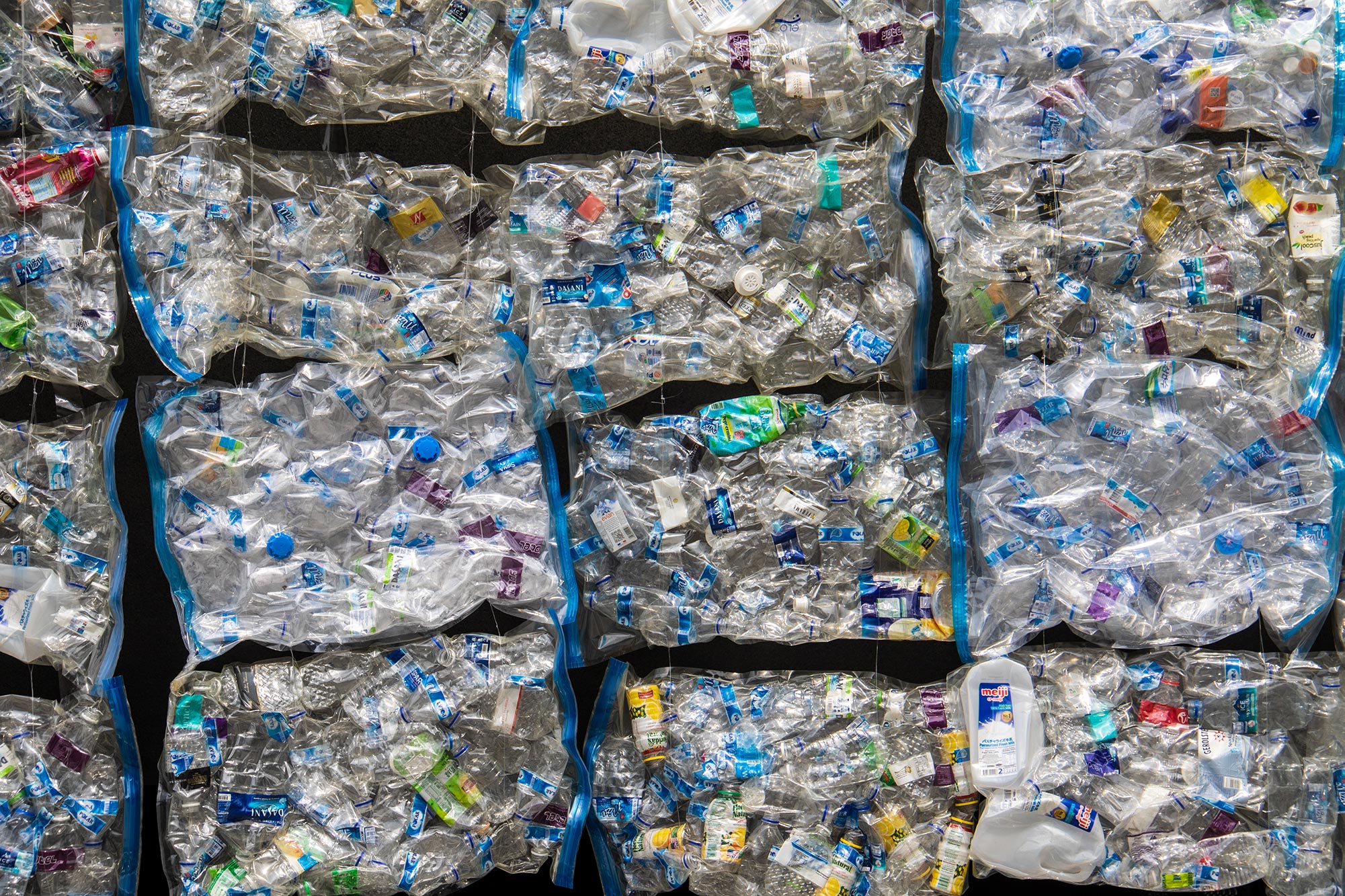
Can plastics recycling be profitable?
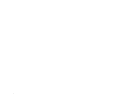
Plastics recycling in industrial areas
plastics, plastics recycling, circular economy, resource wisdom, business cooperation, port, waste, value chain, piloting, reuse
It has become apparent that more plastics need to be recycled. The purpose of this concept is to launch plastic recycling activities in industrial areas and to create cooperation between companies to achieve climate goals. An experiment was carried out to illustrate the functionality of recycling, to obtain information about the volumes of plastics and to collect feedback from companies in Vuosaari Harbour.
- 6443 kg/year: the theoretical amount of plastic waste generated in Vuosaari Harbour.
- 80% of the collected plastics could be reused instead of being used to produce energy according to the pilot project.
- Emissions: carbon dioxide emissions are significantly lower in recycling-oriented solutions than in the current solution in which plastic waste is mainly burnt.
This solution is suitable for
- cities that want to encourage companies to do their bit for climate change;
- companies that want to start recycling their waste or improve their existing procedures;
- companies that are looking for new business opportunities in the recycling sector.
BASIC FACTS
- Location: Vuosaari Harbour, Helsinki
- Life cycle: active phase.
- Organisers: Satu Pasanen/VTT Technical Research Centre of Finland, Juha Hakala/VTT Technical Research Centre of Finland, Saara Pellikka/City of Helsinki.
- Time span: 3 months – 1 year.
- A ‘plastic pilot’, a joint experiment to collect plastic waste from companies, was carried out during the concept development phase. Packaging plastics and plastics from logistics operations were collected from companies in Vuosaari Harbour. The pilot project was carried out in cooperation with the City of Helsinki and the Port of Helsinki between 16 November and 31 December 2020.
- The recycling solutions were compared to the current ones from the perspective of the economy and carbon emissions.
- The concept encourages the reuse of plastics.
The first plastic recycling concept in Vuosaari Harbour
National and international targets, such as the plastics roadmap for Finland and the EU plastics strategy, accelerate the recycling of plastics. The concept was inspired by the enthusiasm of companies in Vuosaari Harbour for recycling – it started at the grassroots level. The purpose of the concept is primarily to start collecting plastics in the industrial area and, secondarily, to promote cooperation between competing companies to achieve the climate goals.
During the conceptualisation phase, a pilot project was carried out in collaboration with public-sector operators, companies and a research institute. Practical experiments such as this produce scientifically valid and pragmatic data, encourage companies to try new work methods and increase dialogue between cities and businesses.
Piloting provides facts for conceptualisation
A ‘plastic pilot’, a joint experiment to collect plastic waste from companies, was carried out during the concept development phase. Packaging plastics and plastics from logistics operations were collected from companies in Vuosaari Harbour. The pilot project was carried out in cooperation with the City of Helsinki and the Port of Helsinki between 16 November and 31 December 2020. Seven logistics companies took part. Plastic material was collected in a waste compactor equipped with a smart scale, which was on loan from Europress Group Oy for the duration of the test.
A total of 812 kg of various types of plastics was collected, mainly polyethylene (LDPE) and polypropylene (PP), which were taken to be reused. The plastic materials were sufficiently clean for the purposes of the collection experiment. Participants filled in a questionnaire afterwards that collected feedback and user experiences for concept development. Most participants found it easy to take part in the plastic pilot and joint collection efforts. Companies thought that collaboration was viable, especially with regard to waste management and other environmental services.
Comparative information with economic and environmental perspectives
The economic perspective was illustrated and assessed in the context of Vuosaari Harbour’s location and the pilot carried out there. Different solutions were created for this industrial area in terms of waste management and recycling, and in addition to the current situation, two alternative solutions are presented, A and B. In the current situation (REF), plastic waste is not recycled but is sent to be burnt at a waste-to-energy facility. Solution A does not involve sorting at the place of origin but all plastic waste is put together and taken to a recycling company. In solution B, plastic waste is sorted at the place of origin, i.e. only LDPE and PP plastic waste is collected.
The results show that the current situation (REF) is the cheapest if only 6.5 tonnes of plastic waste is generated per year, but this option becomes the most expensive as the amount of waste increases. Solutions A and B, which encourage people to recycle, are more economical when the volume is 1.5–2 times higher. Carbon emissions in solutions A and B are significantly lower than in the reference situation. An increase in the amount of plastic waste in solutions A and B generates lower level of emissions than the reference situation.
Putting the concept into practice
The concept is based on solution B, in which the LDPE and PP waste collected from the companies in the port is sent to mechanical recycling. There is also already an industrial recycling solution. As it develops, the concept aims to apply solution A, in which a wider variety of plastic waste can be collected and sent either to be reused as recycled material or as material for the petrochemical industry. Introducing solution A will require cooperation with a suitable recycling or sorting company located near the industrial area. In both solutions, the flow of plastic waste from nearby areas is added to the flow from the port as this increases the impact on the local area. The concept is based on the idea that plastic waste generated in the area is returned there in products used in the area (e.g. packaging films or bags) or is used in products such as fuels used by machines in the area.
All respondents said that a joint collection of plastics should remain a permanent part of the port’s operations. The joint collection model is easy to adopt and scale to suit different types of industrial areas. Expanded to cover the whole country, this type of activity in industrial areas would have the potential for substantial emissions reductions.
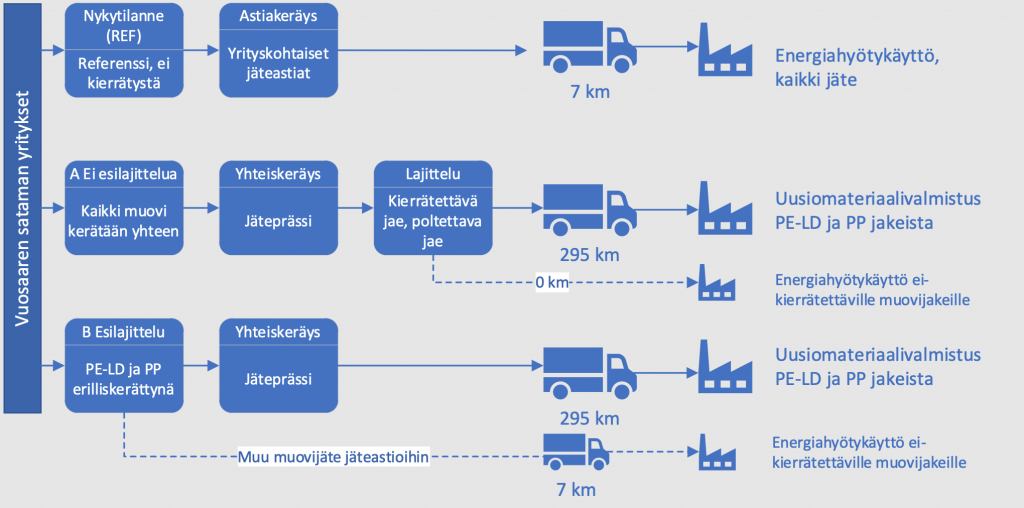
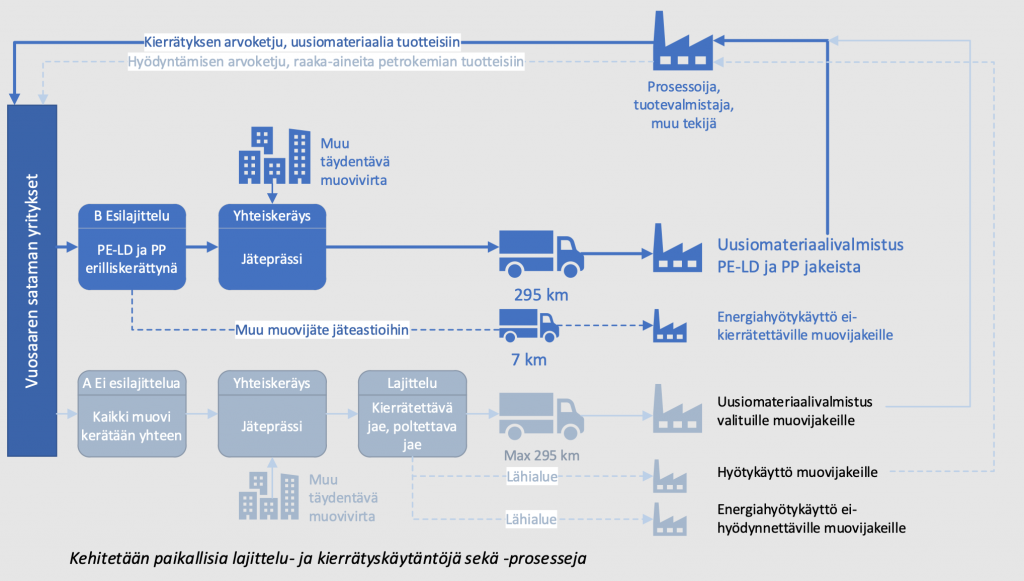
TAKE-HOME MESSAGES
- Companies are enthusiastic about plastic recycling and they want their operations to be more sustainable.
- Piloting provides scientifically valid, practical information on the amount of waste generated in an area and companies’ recycling-related requirements and practices.
- Competing companies can collaborate and gain environmental and economic benefits.
- Cities will be able to persuade companies to adapt the climate goals by launching new pilot projects that focus on emissions reductions and resource wisdom and that benefit companies in the short or long term.
“As the global use of plastics increases, we need recycling to curb this trend. Solutions are created at the local, national and international level. Recycling captures plastic waste for reuse or recovery and offers environmental and economic benefits to businesses.”
– Satu Pasanen, Research Scientist, Circular Economy Developer, VTT Technical Research Centre of Finland
Download
Links
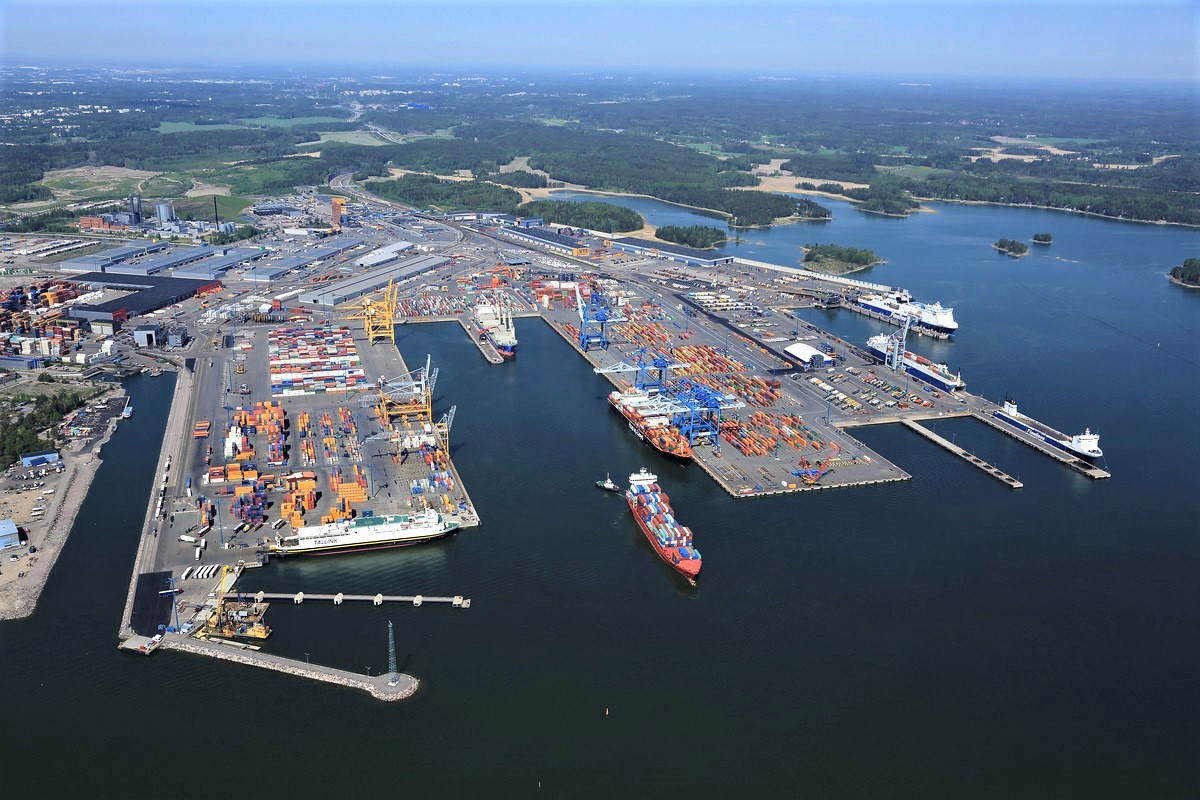
How can machinery contribute to creating a carbon neutral port?
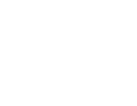
Low-carbon solutions for machinery in cargo port operations at Vuosaari Harbour
machine emissions, cargo port, freight transport, alternative sources of power, road map
The model explored ways to reduce carbon emissions from machines used in cargo port operations, using Vuosaari Harbour in Helsinki as an example. The key themes were low-carbon power sources, the contribution of different partners and the roadmap for reducing emissions from machine operations.
- More than 75% of the CO2 emissions from machines in Vuosaari Harbour are generated by straddle carriers and terminal tractors, so measures to reduce emissions should focus on these types of machines.
- Electrification would appear to be both an emission- and cost-effective solution for energy-intensive machines with high utilisation rates, such as straddle carriers.
- A pilot programme for new technologies has been proposed for 2021–2027, which would pave the way for the launch of low-carbon solutions to the market.
This solution is right for you if
- you are interested in ways and means of reducing carbon emissions from machines, especially in the context of cargo ports;
- you are working on reducing carbon emissions from port machines or port operations;
- you want to promote low-carbon machines in a company or in an industrial area.
BASIC FACTS
- Location: Vuosaari Harbour, Eastern Helsinki
- Time span: 2019–2021
- Organisers: Saara Pellikka from the City of Helsinki’s environmental services was responsible for implementing the concept in close cooperation with VTT Technical Research Centre of Finland, the Port of Helsinki and the following key partners: Finnsteve Oy Ab, Steveco Oy, Multi-Link Terminals Ltd Oy, Oy M. Rauanheimo Ab / Oy Adolf Lahti Yxpila Ab, Container-Depot Ltd Oy / Arctic Container Oy, SA-TU Logistics Oy, Nurminen Logistics Oyj, Alfons Håkans, Konecranes Finland, Kalmar / Cargotec, Royal Terberg Group and Port of Gothenburg (reference site).
Companies interviewed to canvass their commitment and areas for development
The City of Helsinki’s environmental services interviewed companies in Vuosaari Harbour in late 2019 and early 2020 to explore areas for improvement in terms of reducing emissions from machines. A key finding was that companies want to reduce emissions from machinery, but new solutions need to be cost-effective and easy to operate in the port environment. Biofuels and electrification, in particular, were brought up as potential means to achieve this. A summary was prepared on the basis of the interviews, and the following measures were proposed:
- Increasing companies’ understanding of new power sources and emissions reduction solutions that are suitable for port operations (including emission- and cost-efficiency).
- Exploring the types of control measures that the Port of Helsinki could use to encourage companies that operate in the area to use new power systems, and assessing the infrastructure capacity and the necessary changes if a new source of power were to be adopted on a large scale.
The report describes how the emission targets for machines can be achieved
VTT examined measures that would reduce CO2 emissions from the port’s machines by 60% by 2035 (in Finnish: Selvitys ja tiekartta Vuosaaren sataman työkoneliikenteen päästövähennyksille). The study suggests that measures should focus on straddle carriers and terminal tractors, as these types of machine were estimated to generate more than three-quarters of emissions from machines in the area.
It would seem impossible to meet the emission targets without some degree of electrification of the straddle carriers or use of renewable fuel. Electrification proved to be a cost-effective solution for energy-intensive machines with a high utilisation rate, such as straddle carriers. The power grid in the port area would appear to be sufficient for operating battery-operated straddle carriers and terminal tractors. The simultaneous operation of the port’s 33 straddle carriers would require approximately nine 600 kW fast charging points, which would mean an investment of approximately 3–5 million euros.
Incentives for the Port of Helsinki would include compensation for the additional cost of renewable fuel, a discount based on the utilisation rate of electrical machinery and leasing electrical machines and charging infrastructure to operators for testing purposes. The roadmap for emissions reductions in 2021–2035 was presented as a key output.
Piloting of new technologies is at the heart of the carbon roadmap
The carbon roadmap for machine logistics paves a way for the use of market-based low-carbon solutions in the Vuosaari Harbour area. It was proposed that a pilot project should be launched to make it easier for port operators to switch to fully electric machinery and start using renewable fuel so that they could learn how to use new technologies. Operators would test some electric machines, such as straddle carriers and terminal tractors, and the use of renewable fuel in machines of different ages would also be demonstrated in the project. The path to low-carbon machines would have three phases:
- Pre-planning of the piloting project, 2021–2022
- Piloting new technologies, 2022–2027
- Gradual transition to market-based operations, 2027–2035
The roadmap was drawn up by VTT as part of the study and roadmap project on emissions reductions in Vuosaari Harbour.
Machinery emission calculation using a calculation model and training video
The Excel-based calculation model can be used to calculate the carbon emissions and total operating costs of machines and to compare the cost-effectiveness of emissions reduction with different power source options (EUR/tonnes of CO2). The model takes into account both direct emissions (TTW, tank-to-wheel) and lifecycle emissions (WTW, well-to-wheel) from machines. The model is particularly suitable for stevedoring companies that own port machinery, but it can also be applied to other types of machinery, provided that input data is added. The model has two parts:
- The generic model that calculates emissions and costs for an individual year.
- The scenario model that includes the generic model and also calculates emissions for 2019–2035.
The calculation model and an introductory video have been made by VTT as part of the study and roadmap project on emissions reductions in Vuosaari Harbour.
Training video on the use of the model for calculating emissions and costs generated by machines (in Finnish):
TAKE-HOME MESSAGES
- The port environment has special requirements and offers opportunities for measures to reduce emissions from machines.
- The most suitable emissions reduction solutions are found by optimising them according to how much a machine is used and how practical as well as emission- and cost-efficient they are.
- Piloting would make it possible to find the most efficient technologies, operating methods and service models for the port environment, and it would pave the way for the launch of new low-carbon solutions to the market.
“The goal of the Port of Helsinki is to reduce CO2 emissions in the entire port area by approximately 30,000 tonnes by 2035. All operators in the port area need to work together to reduce emissions. The roadmap provided by the HNRY project is a great tool for exploring potential ways to reduce emissions generated by machines in the port area.”
– Andreas Slotte, Head of Sustainable Development, Port of Helsinki Ltd.
Download
Links
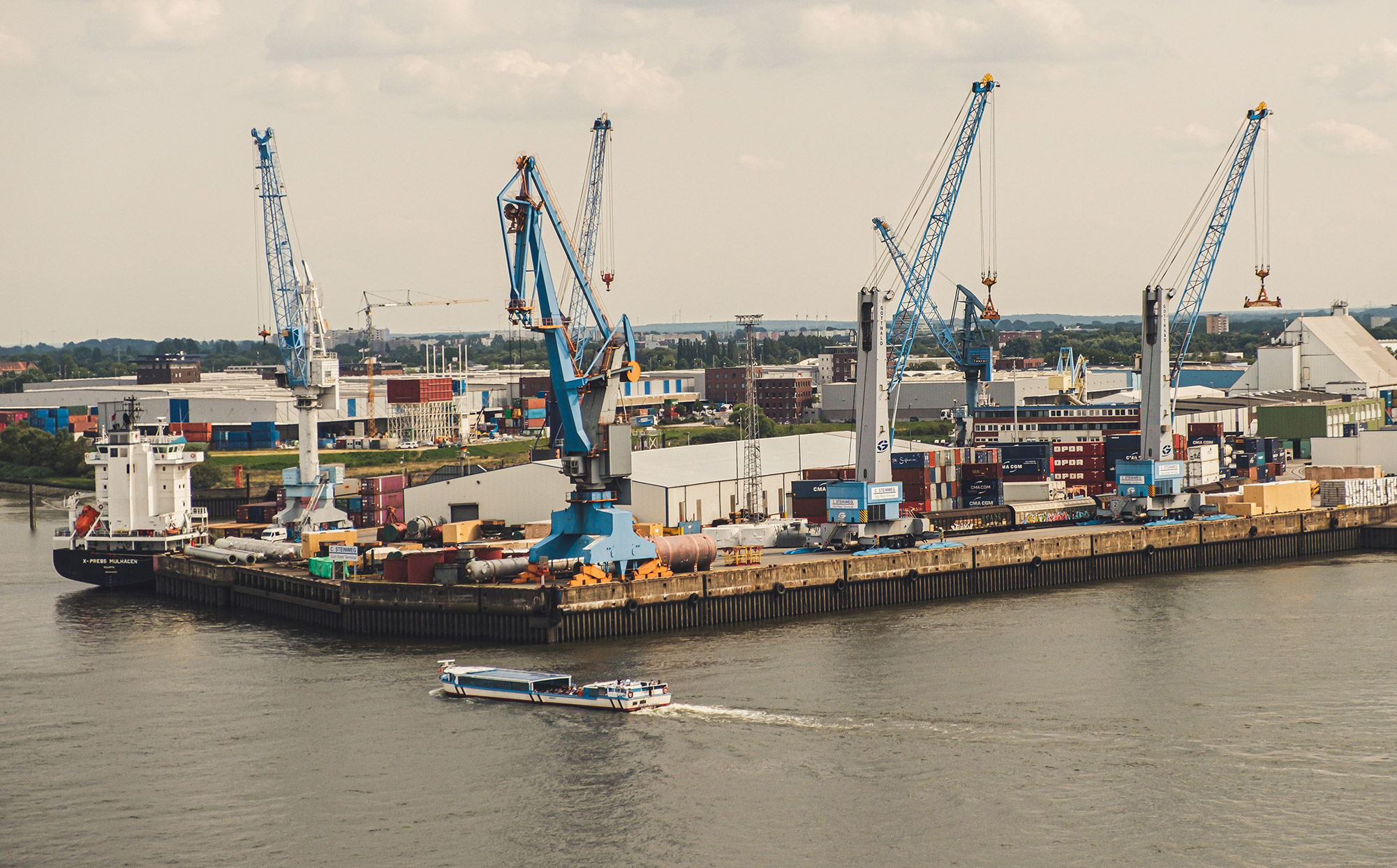
Is carbon neutrality and resource wisdom in a gated industrial area too narrow a perspective?
A resource-wise and carbon-neutral maritime industry network
reduce, reuse, recycle
The project developed an optimal operating model for flows of materials, resources and information in the Blue Industry Park and Turku Shipyard. The model can be used to achieve resource wisdom and carbon neutrality throughout the supply chain.
- 20–30% increase in value-adding operations.
- 3–7% reduction in material loss.
- 20% better production turnaround time through supply chain transparency and management.
- 5% lower material costs through centralised procurement.
This solution is right for you if
- you operate in the supply chain of Turku Shipyard;
- you operate in a manufacturing industry supply chain;
- you want to streamline your supply chain operations.
BASIC FACTS
- Location: Perno district, Turku. Next to Turku Shipyard.
- Industrial area life cycle: planning phase
- Organiser: Blue Industry Park Oy.
- Time span: 5–10 years from 2021 onwards.
- 600 companies in the supplier network.
- The maritime industry network in southwestern Finland employs 11,000 people.
- The turnover of the maritime industry network was EUR 3.3 billion in 2019.
The aim is to increase the efficiency of the maritime industry network
The concept identified how the operations of the maritime industry network could be streamlined, and an operating model was created for the planning and implementation of these improvements. The aim was to optimise the material, resource and information flows between the Blue Industry Park (BIP) and Turku Shipyard. The project assessed what kind of operating methods the companies in the maritime industry network should use in order to make the network’s operations as resource-wise and carbon-neutral as possible. Finally, it was determined what kind of control system would support resource-wise and carbon-neutral operations.
The logistics centre offers the best support to resource-wise and carbon-neutral operations
The concept determined which activities should be located in the BIP area in order to make the maritime industry network as efficient as possible and to support resource-wise activities. The key functionalities were production facilities and the logistics centre.
The need for production facilities varies: some operators require a small workshop while others need a larger production facility. The premises to be built must also be adaptable so that they can meet the changing demand. Pre-assembly and modularisation would also reduce the logistical burden in terms of traffic volumes and packaging materials. Traffic volumes are reduced when larger entities are transported and there are fewer deliveries of parts and components in the area.
Recycling reduces material waste
Recycling packaging waste and standardising transport packaging in the area would be very beneficial. If standardised methods were used for recyclable packaging materials, logistics operations would be clearer and the volume of packaging materials in the area would be reduced.
Building a centralised recycling centre in the BIP would serve companies in the area and help ensure that waste materials are recycled. The recycling centre would operate in the area between the BIP and the shipyard, which would be ideal for all parties.
With regard to the location of functionalities, traffic going into the shipyard must also be considered. The logistics centre should be located either beside or in the immediate vicinity of the production facilities in order to avoid any unnecessary traffic.
Information creates trust
Yhteistoiminnan ja resurssiviisauden edistämiseksi tarvitaan mitattua tietoa. Konseptiin liittyen määriteltiin viisi tärkeitä mittaria:
Measured data is required to promote collaboration and resource wisdom. Five important indicators were identified in relation to the concept:
- Security of supply of incoming materials
- DIFOT (Delivered In Full and On Time)
- Security of supply of site-specific material packages
- DIFOT (Delivered In Full and On Time)
- Progress of the site-specific plan
- Timing and accuracy of master production scheduling
- Timing and accuracy of detailed planning
- Implementation of the plan content
- Monitoring deviations
- Work package-specific monitoring
- Delivery line-specific monitoring
- Monitoring of transport volumes
- Monitoring of inbound logistics
- Monitoring of reverse logistics and material loss, surplus/waste
- 3R strategy (Reduce, Reuse, Recycle)
TAKE-HOME MESSAGES
- Material wisdom: centralised materials management can reduce material waste.
- Resource wisdom: minimising the amount of surplus material with more careful planning.
- Information wisdom: the information flow generated by the digital platform enables supply chain management and development.
“Stopping structural waste is the only way to save the planet.”
–Ari Viitanen, HPJ CarinaFour
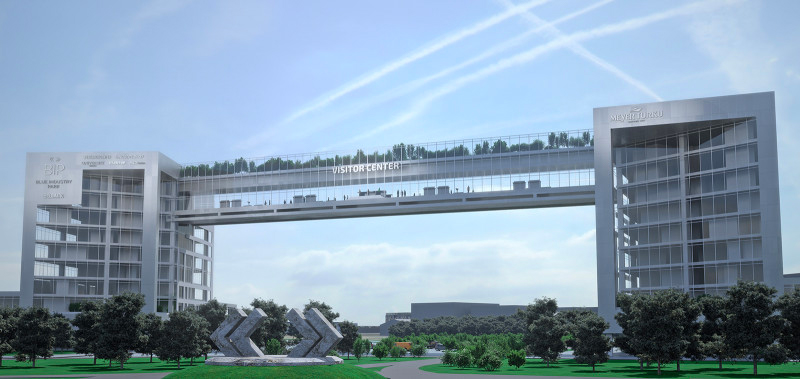
How to create a new resource-wise and carbon-neutral industrial area?
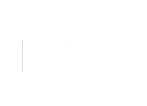
Blue Industry Park: the new resource-wise and carbon-neutral industrial area
hiilineutraali teollisuusalue
When building a carbon-neutral and resource-wise industrial area, it is necessary to take into account not only the planning but also the construction of the area and its day-to-day operations. The Blue Industry Park is an area that is gradually being built beside the Turku Shipyard, and it will be a functioning ecosystem of manufacturing industries and service operators. It takes the expertise and willing of all companies to achieve resource wisdom and carbon neutrality in the area.
- Blue Industry Park Oy. Established during the project to lead the construction of the area.
- Great transport links. Deep-water channel, E18, railway and distance to the airport 10 km.
- 55 hectares. Total area
This solution is right for you if
- you operate in the supply chain of Turku Shipyard;
- you operate in a manufacturing industry supply chain;
- you want to streamline your supply chain operations;
- you are planning a carbon-neutral and resource-wise industrial area;
- you are a contractor or developer in a carbon-neutral and resource-wise industrial area;
- you are a public operator, such as a planning officer, and you want to know how carbon neutrality and resource wisdom are implemented.
BASIC FACTS
- Location: Perno district, Turku. Next to Turku Shipyard.
- Industrial area life cycle: planning phase
- Organiser: Blue Industry Park Oy.
- Time span: 5–10 years from 2021 onwards.
- The maritime industry network in southwestern Finland employs 11,000 people.
- The value of Turku Shipyard’s order book in Q1/2021 is EUR 6.5 billion, cruise ship deliveries until 2026.
Towards a sustainable future
Blue Industry Park is a close-knit and diverse community of companies and research institutes, which are leading the change. There are no limits to its growth opportunities. The scalable spaces and shared resources provided in the area reduce the need for non-essential investments and enable business development in a sustainable and commercially viable manner. The community is responding to megatrends of production modularity and circular economy on a scope never seen before.
New technologies and cooperation are prerequisites for success
The concept guidelines do not provide ready-made solutions for the future, but they encourage all parties to share their expertise to achieve the shared goal. For the area to be successful, the best and most sustainable technologies and operating models available must be applied in every phase and solution.
The guidelines cover solutions for design and civil engineering, buildings and operations as well as transport.
Blue Industry Park’s ecosystem also includes service companies such as occupational health care, lunch restaurants and a visitor centre. Renewable energy sources are preferred, of course, and carbon neutrality is achieved by combining several solutions.
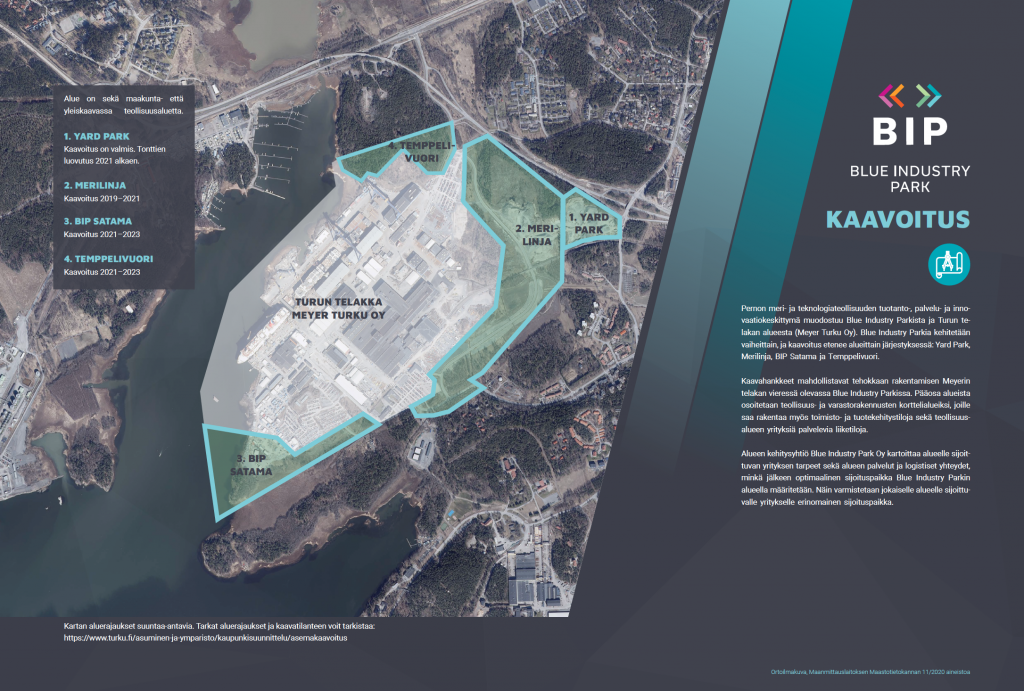
Research collaboration with universities
It is valuable for companies operating in the area that there are four institutes of higher education in Turku with research related to the maritime industry and maritime logistics. Blue Industry Park is a platform for productive cooperation in research projects and the supply of skilled labour both now and in the future.
The universities in Turku cover disciplines that are relevant to planning and building the area, such as energy technology, structural engineering, circular economy, economics and industrial management engineering.
TAKE-HOME MESSAGES
- The area’s location in relation to existing transport links and major customers is essential to minimise emissions from transport.
- When building the area, the use of land masses in the region and the area under construction must be optimised so that unnecessary transportation and costs can be avoided.
- Renewable energy production, transmission and storage solutions need to be considered at the planning phase.
- The flexibility and modularity of the facilities improve their occupancy rate and cost efficiency.
- Sharing machinery and equipment makes it easier to adopt new eco-friendly technologies and reduces the number of equipment needed in the area.
- There must be a leader with a clear role to create an area that runs on synergy and cooperation.
”Companies must assess and develop their practices: new ideas only come from doing things differently. We know that those who can realise their full growth potential, find the right partners and work in a carbon-neutral and resource-wise manner will be successful.”
– Tero Lahti, CEO, Blue Industry Park Oy.